What Are the Key Differences Between Flammable and Combustible Materials?
If your workplace handles certain hazardous materials, such as flammable chemicals, it’s vital for you to understand the risks they pose. In particular, you must recognise the difference between flammables and combustibles. The level of risk that a material poses and how easily it can cause a fire is often affected by whether it’s flammable or combustible.
This article will clearly define what separates flammable and combustible materials. Knowing this will enable you to better understand their properties so you can handle and store them safely in your workplace.
What is the Difference Between Flammable and Combustible?
Flammable and combustible materials differ based on the temperatures they must be exposed to in order to catch fire. Specifically, flammables will ignite at lower temperatures than combustibles when exposed to an ignition source. This specific temperature, also known as a flash point, is what separates flammables and combustibles.
The flash point is the lowest temperature at which hazardous materials will generate vapours and ignite if exposed to an ignition source.
These temperatures vary from material to material, but there are certain flash point thresholds that separate flammables from combustibles.
What are the Flash Points of Flammables and Combustibles?
Flammable materials | Combustible materials |
---|---|
A material is considered flammable if it has a flash point of any temperature below 37.8 ºC. | A material is considered combustible if it has a flash point higher than 37.8 ºC and below 93.3 ºC. |
Flammable and combustible materials will generate vapours when exposed to a temperature at, or above, its flash point, which can easily ignite when exposed to an ignition source. Therefore, the lower the flash point of a material, the higher the risk is. This is because the temperature of most workplaces will not be above the lowest combustible flash point (37.8 ºC), which means that combustibles won’t start to form vapours in a normal working environment. Oppositely, flammables are more likely to form vapours in normal work environments, because their flash points are lower.
This is why it’s so crucial to know exactly what flammable or combustible materials you have in your workplace, so you can control the risks accordingly. For example, if you have a flammable material with a flash point of 25 ºC, storing it under 25 ºC will prevent it from generating vapours that could ignite. If they have a lower flash point however, such as -20 ºC, then you will need to implement further control measures to prevent existing vapours from igniting.
You can find examples of flammable and combustible materials, as well as their flash points, in the table below.
Flammables | Flash point | Combustibles | Flash point |
---|---|---|---|
Petrol gasoline* | -43 ºC | Diesel fuel* | 52 ºC to 82 ºC |
Ethanol | 16.6 ºC | Phenol | 79 ºC |
Acetone | -20 ºC | Kerosene* | 38 ºC -72 ºC |
Methanol | 12 ºC | Formaldehyde | 64 ºC |
Propylene oxide | -37 ºC | Hydrazine | 52 ºC |
Ethyl chloride | -50 ºC | Paint thinner* | 40 ºC |
Benzene | -11 ºC | Naphthalene | 78.89 ºC |
*Note: this may vary depending on the specific composition.
If your workplace stores or uses any of these, or any other flammable or combustible materials, it’s vital for you to understand how to control their risks. Otherwise, you will leave your workplace susceptible to a fire or even an explosion.
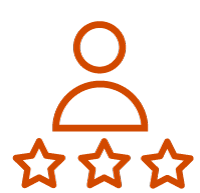
Need a Course?
Our DSEAR Training provides you with a full introduction to the requirements of the regulations and will ensure you understand the risks from dangerous substances and explosive atmospheres, know how to carry out a risk assessment, and can implement suitable workplace control measures.
How Flammable and Combustible Materials Affect Building Safety
It’s essential that you prevent flammables and combustibles from coming into contact with sources of ignition, particularly if the materials can create vapours or an explosive atmosphere. Otherwise, the fire safety of your building could be compromised.
Certain materials will require stricter controls than others to minimise these fire risks, especially depending on their flash point. Therefore, the first step you should take is to check the safety data sheets (SDSs) of every hazardous substance you store on site.
The law requires all hazardous materials to come with safety data sheets. These provide information that helps you to decide what safety procedures are necessary for a certain hazardous material.
The information that SDSs should contain include:
- Identification of the substance or mixture.
- The name, address, and contact details of the manufacturer or supplier.
- Hazard identification of the chemical or chemicals in the substance, including hazards caused by reaction with any other substances.
- Composition details and information on ingredients, including the physical and chemical properties, stability, and reactivity. SDSs should give the flash point of volatile liquids that are classified as flammable.
- Toxicological information, including routes of entry to the body (inhalation, ingestion, skin or eye contact, or other routes).
- Ecological information.
- Accidental release measures.
- Transport, handling, storage, and disposal information.
- Exposure controls, personal protection, and regulatory information.
- First aid and fire-fighting measures.
Under the UK Registration, Evaluation, Authorisation and Restriction of Chemicals (UK REACH) Regulation, manufacturers and suppliers of chemicals must provide safety data sheets with their products. These are international standards and are now in UK law, and apply to almost all chemicals placed on the market. In Northern Ireland, manufacturers and suppliers must meet EU REACH.
Safety data sheets should contain comprehensive information about the material. Employers and workers should use this as a source of information about hazards and safety precautions. However, it is important to remember that they are not substitutes for risk assessments. Rather, they will help to inform the risk assessment. SDSs provide key information helping the competent person undertaking the workplace risk assessment determine what specific safety measures should be put in place for the materials in your workplace.
Your workplace risk assessment, supported by the information outlined in any SDSs for the materials in your workplace, should help you determine if you need to:
Substitute materials for less volatile alternatives.
Substitution is one of the first steps in the hierarchy of control. Therefore, wherever possible, you should replace the hazardous substance with one that is non-hazardous (or less hazardous if it is not reasonably practicable to use a non-hazardous substitute). A non-hazardous alternative must always be selected first, if possible.
Additionally, the processes used can also be changed to prevent the risks from hazardous substances altogether.
Reduce the quantity of materials that your workplace holds.
Your workplace should only ever hold the minimum necessary to keep the business running. Do not overstock, as this can worsen the fallout of an accident.
Store all hazardous materials with compatible substances.
Never store incompatible substances together as it can worsen the fallout in the event of a fire.
Check that there are suitable engineering controls.
Wherever your workplace stores hazardous chemicals, ventilation (such as local exhaust ventilation or general mechanical ventilation) is crucial for safely removing hazardous substances from the workplace atmosphere. This minimises the chance of them setting on fire. Other examples of engineering controls including segregating work areas where hazardous substances are used or generated, and providing refuges for operators.
Ensure the storage area is appropriate.
Make sure you keep hazardous materials in a location with suitable fire resistance and never exceed maximum capacities. It’s crucial to store flammables and combustibles in non-conductive, sealed containers (such as glass or plastic). If this is not possible, containers must be appropriately grounded to prevent static charge. Furthermore, you must keep any potential sources of ignition away from the storage area and ensure the doors of storage rooms and cabinets are kept closed.
Control the temperature of the storage facilities.
If you control the temperature of the area to limit vapours, make sure you monitor this closely. You should also store all containers out of direct sunlight.
Ensure safe systems of work are enforced and safe working procedures are followed.
Safe systems of work are usually a combination of various control measures that are enforced to ensure health risks are reduced, where prevention of exposure is not reasonably practicable. A safe system of work may be a combination of engineering controls, safe operating procedures, supervision, and staff training, for example.
All staff must be competent in their duties and must follow safe working procedures for storage, transport, handling and use of hazardous substances. For example, staff must follow their workplace’s decanting process to ensure they don’t cause spills. More specifically, hazardous substances in their original containers until the point of use, they must keep incompatible substances segregated, and, where necessary, only ever decant into properly labelled, suitable containers. You must never use homemade or unlabelled containers, or reuse containers for multiple substances.
Use any necessary personal protective equipment (PPE).
Personal protective equipment, or PPE, refers to equipment that is intended to be worn or held by a person at work to protect them from health and safety risks. PPE should only be used as a last resort after all other controls have been considered. PPE, such as anti-static footwear and clothing, may be required to help mitigate any residual risks.
Improve the fabric of the building.
In some cases, the materials of your building could pose a significant fire risk. A notable example can be seen in the Grenfell Tower tragedy, which was made significantly worse by the unsafe aluminium composite material (ACM) cladding. As of 2018, the government have banned this combustible material, as it poses a major fire risk. If yours has this type of cladding, the building owner must replace it.
As long as you recognise the different safety requirements of flammable and combustible materials, you can easily minimise fire safety risks in your workplace. Always pay attention to the SDSs and follow any training provided to you regarding hazardous materials.
What to Read Next:
- Understanding DSEAR: Area Classification and Hazardous Substances
- What is a COSHH Assessment?
- What is a Spill Kit? Contents Checklist
- DSEAR Training Course
- Accident and Incident Investigation Course