PAT Testing for Home Workers
With a large number of businesses adopting a remote-first approach permanently, choosing to work from home is an increasingly popular choice. However, it’s important that employers recognise that they have the same legal duty to protect the health and safety of employees who work from home. Additional measures will likely need to be put in place to ensure this, particularly to make electrical equipment safe to work with. One method they may use is PAT testing, and it’s important for everyone to be aware of what this is and when it may be used.
This article will discuss whether there are PAT testing regulations in the UK, the duties employers have surrounding electrical safety, whether PAT testing should be carried out for home working, and how workers might check their electrical equipment.
What is PAT Testing?
PAT refers to portable appliance testing, a simple test carried out to ensure that portable electric equipment is operating safely. Portable electrical equipment is any item of electric equipment that can be carried or moved around manually, whether it’s connected or disconnected from an electrical supply. Therefore, it includes a variety of equipment which home workers may use – computers, laptops, desk lamps, printers, etc.
PAT testing is an example of combined inspections and tests that are carried out if electrical faults can’t be detected by visual inspection alone. In particular, they are used for Class I portable appliances. PAT testing must be carried out by someone who is competent and trained to do these types of tests.
Are There PAT Testing Regulations in the UK?
PAT testing isn’t required by law in the UK; rather, it’s one way of checking equipment’s electrical safety. While there are no UK PAT Testing Regulations, employers have a legal duty to ensure that electrical equipment is safe under other legislation.
Under the Health and Safety at Work etc. Act 1974, employers must protect the health, safety, and wellbeing of employees as far as is reasonably practicable. Ensuring that there are arrangements to inspect and maintain work equipment, such as portable electric appliances, in a safe condition at all times is included in this. Employers also have a duty to ensure that ‘suitable and sufficient’ risk assessments are carried out, as required under the Management of Health and Safety at Work Regulations 1999 (MHSWR). Again, as part of this, the use and maintenance of portable electric equipment should be considered, including for any home workers.
Furthermore, Regulation 6 of the Provision and Use of Work Equipment Regulations (PUWER) 1998 requires work equipment to receive inspections and tests where necessary for maintaining its safety. The regulation states:
Every employer shall ensure that work equipment exposed to conditions causing deterioration which is liable to result in dangerous situations is inspected (a) at suitable intervals; and (b) each time that exceptional circumstances which are liable to jeopardise the safety of the work equipment have occurred, to ensure that health and safety conditions are maintained and that any deterioration can be detected and remedied in good time.
Regulation 6, The Provision and Use of Work Equipment Regulation 1998
The frequency at which this must be carried out depends on several factors, so will be determined via the risk assessment, with consultation of manufacturers’ guidance, and any other relevant information. PAT is not legally required to fulfil this duty, but rather is one suitable way of doing so.
More specifically, the Electricity at Work Regulations 1989 require that any electrical equipment with the potential to cause injury is maintained in a safe condition. They do not specify how this will need to be achieved, or how frequently any inspections or tests need to be carried out, as this depends on the equipment itself and its usage.
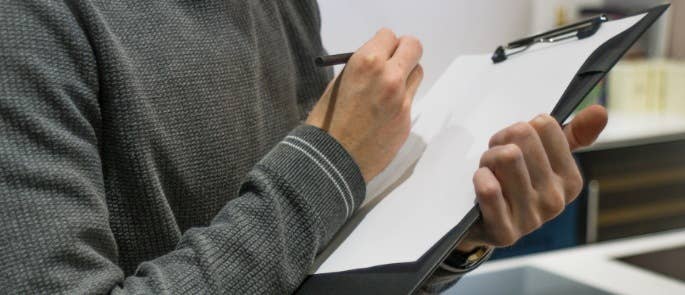
How Often is PAT Testing Recommended?
The law doesn’t say how often electrical equipment should undergo PAT testing, including for home workers’ equipment. Instead, employers, or those who are competent that they have delegated the responsibility to, will determine how often equipment should be PAT tested. To do this, they should consult the risk assessment, refer to manufacturer’s guidance, information provided by the HSE, any specialist input, and anything else they identify as relevant and necessary to aid their decision.
While there aren’t strict requirements for the frequency of PAT testing, the HSE guidance ‘Maintaining Portable Electric Equipment in Low Risk Environments’ contains advice on inspection and test frequencies. The frequency of inspection and testing that is advised depends on the type of equipment, the environment it is used in, and how it’s used.
For example, the suggested initial intervals for combined inspection and testing (PAT) of desktop computers and VDU (visual display unit) screens is up to five years, unless the equipment is double insulated (in which case, PAT testing isn’t suggested).
Employers may determine that their home workers are at a higher risk of danger from portable or movable electrical equipment compared to employees who don’t work remotely. As a result, they may decide to implement a more frequent programme of PAT testing for electrical equipment used by home workers.
Who is Responsible for PAT Testing?
As mentioned, employers have a legal duty to ensure that any electrical equipment that has the potential to cause injury is maintained in a safe condition. This may include ensuring that PAT testing is carried out, if identified by the risk assessment as a suitable way to ensure safety.
If PAT testing takes place, it must be carried out by someone with the necessary knowledge and experience who has the right equipment for the task. They don’t need to be an electrician but the individual must know how to use the equipment and how to interpret the results.
It is important that all electrical equipment receives frequent user checks and visual inspections, including those which don’t need to undergo PAT testing. For simple, low-risk equipment, home workers will likely be able to safely carry out user checks themselves. Employers must ensure that workers understand and carry out regular checks on both equipment that they supply and any of their own personal electrical equipment used for work. If employers provide new work equipment for home working, they must ensure that it meets the electrical requirements for safety and that it comes with the manufacturer’s instructions.
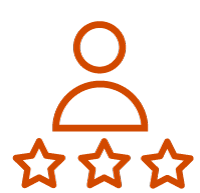
Looking for PAT Testing Training?
If you’re looking for an awareness level of knowledge of PAT and will be conducting PAT Tests in a low-risk environment, our Portable Appliance Testing (PAT) course may be suitable for your needs.
Should PAT Testing Be Carried Out for Home Working?
Remote working can create more of a barrier to ensuring that home workers’ electrical equipment remains safe for them to use. However, employers must protect all of their employees from harm while they are at work. If electrical equipment isn’t checked and maintained properly, there may be an increased risk of electrocution, electric shock, and electrically-initiated fires. Carrying out user checks, formal visual inspections, and, where necessary, combined inspection and testing (PAT) of electrical equipment will reduce the risk of these types of incidents happening.
Employers are responsible for ensuring that any equipment used by their employees who work at home is safe and without risks, including electrical equipment. They have the same legal obligations towards home working employees as they do for employees who don’t work remotely. While PAT testing isn’t a legal requirement, it may be carried out on some types of work equipment as part of the overall electrical safety considerations.
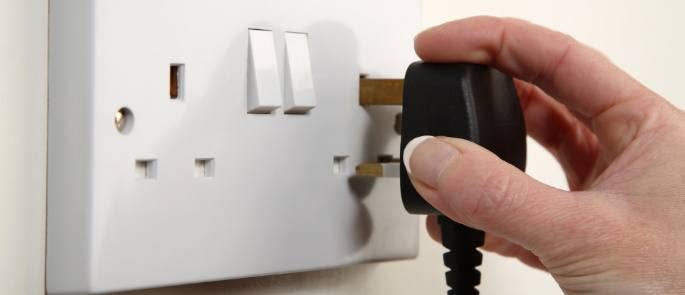
Most employees won’t be carrying out PAT testing of their equipment themselves as they will not have the necessary knowledge and experience. Employers are responsible for putting in place a process to ensure that any electrical equipment that should be PAT tested, including the equipment of home workers, undergoes the necessary testing.
This may involve sending someone who has been properly trained to check the equipment periodically, or for the equipment to be taken to or sent to the office, or other workplace, where relevant.
As well as electrical hazards, there are many other risks associated with home working. This includes the risk of developing musculoskeletal disorders (MSDs) from incorrect DSE use or poor manual handling, or injuries sustained from slips, trips, or falls due to obstructions. You can find out more about these and download our Risk Assessment for Home Working Template in one of our other articles, here.
How Can Home Workers Check Equipment’s Electrical Safety?
Employers of home workers have a duty to maintain any equipment used for work purposes. Employers must ensure that those who use electrical equipment have received sufficient instruction, information and, where necessary, training. Specific training will be required for anyone who maintains electrical equipment and that any work requiring electrical knowledge should only be carried out by someone competent in electrical work.
Home workers who use electrical equipment have a responsibility to help ensure safety, which involves the following:
- Use electrical equipment for its intended use.
- Stop using and unplug equipment immediately if it’s faulty. Report any issues or faults to the relevant person immediately.
- Carry out simple user checks before using the equipment, as advised by their employer.
- Consult the user manual that accompanies the equipment and adhere to it.
- Switch off equipment and power sockets when not in use.
- Avoid overloading extension sockets with multiple appliances, and never daisy chain extension leads.
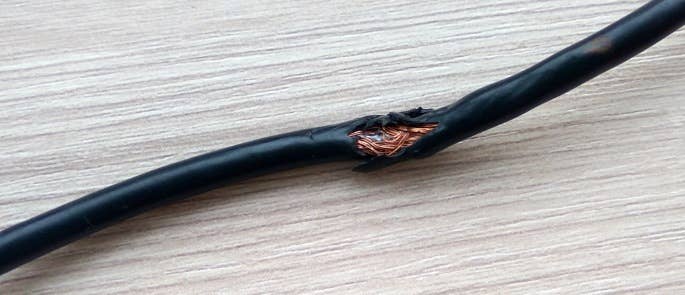
User checks, or pre-use checks, should be carried out by the users of equipment before operation. It should involve looking for obvious defects or faults, such as damaged wires, and making sure that the equipment is safe to use. With some instruction, home workers will be able to carry out this type of check of their equipment. Our article ‘Can I PAT Test My Own Equipment?’ contains further guidance on how you can carry out a user check.
If workers notice that any of their electrical equipment isn’t working properly or is damaged, they must stop using it, unplug the device and then immediately alert their manager or supervisor. The manager or supervisor must arrange for maintenance and repairs where necessary.
While PAT testing isn’t required by law, any electrical equipment that is used by employees, including for home working, must be maintained in a safe working condition, and PAT testing may be included as part of this. Employers are responsible for putting in place measures which protect their employees from harm, and should provide employees with information on how PAT testing for home workers may be carried out, as well as how to carry out user checks of their equipment, to ensure the overall safety of electrical equipment.
Further Resources:
- Portable Appliance Testing (PAT) Course
- Weekly Working From Home Structure: Free Schedule Template
- Risk Assessment for Working From Home
- Work-Related Musculoskeletal Disorders