Preventative Maintenance in the Food Industry
The HACCP (hazard analysis and critical control points) system requires food processing plants to maintain food manufacturing equipment. The most efficient plants opt for a combination of preventative, reactive, proactive, and predictive approaches.
All these approaches are valid, but each has a few pros and cons. This article looks at preventive maintenance which, when done right, is a time and cost saving process. Preventive maintenance can also reduce machine downtime, prevent and minimise damage, and extend the useful life of the equipment.
This article looks at the importance of equipment maintenance and maintenance logs, including a checklist and template to help you plan equipment maintenance.
Importance of Equipment Maintenance
An effective maintenance routine makes sure that operations continue, repair costs are minimised, and downtime is reduced.
Preventative maintenance is the checking of machines and equipment on a planned, regular basis. The aim is to prevent costly downtime and lessen the likelihood of faults. It requires more planning and effort than other methods – but has long and short-term benefits in cost-reduction and efficiency of machine performance.
Preventative checks are made before a machine breaks and while it is still running. Generally, the strategy leads to good food hygiene and prevents foreign materials entering food produce.
Plants that use the preventative method have a far greater chance of catching and correcting issues before they become problems. The method uses a fair amount of labour time to perform the checks – but it pays off.
Organisations that use the preventative method, check machines at specified time intervals. This method tends to save energy as machines are maintained at a peak level of performance.
Other Maintenance Approaches
Reactive Maintenance is a method where machines run until they fail. It’s a hands-off approach (which can’t really be called a strategy), and the big benefit is that it keeps routine maintenance costs low. But, and here’s the big but, it tends to be costly in the long run.
Organisations who use this method find that costs arise in other areas. So when a machine fails without warning, the plant has a lot of expensive downtime. Also, it’s likely that the downtime will increase labour costs to get the machine operational again. Making it, all in all, an inefficient method.
Predictive Maintenance uses advanced technology such as infrared and ultrasound equipment during the routine inspection of machines. NASA claims that the method can stop unexpected breakdowns and by using advanced tech, factories can minimise the amount of time needed to inspect equipment piece by piece.
This method checks machine health and the data provided allows the person accessing the machine to estimate when repairs are going to be needed and to predict when a failure might happen. The bad news is that equipment like the ‘Ultraprobe’ are expensive, but if you’re willing to fork out, this method accurately stays a step in front of faults.
Proactive Maintenance is a systemic issue-focused maintenance program. Rather than examining equipment, this approach considers how to control the problems that lead to machine wear and tear as opposed to the deterioration itself.
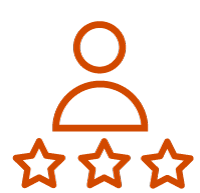
Need a Course?
Our Good Manufacturing Practice (GMP) Course provides learners with a thorough understanding of food hygiene practices that are specific to food manufacturing premises, focusing on the specific day-to-day processes in a food or drink factory.
Preventative Maintenance Procedures
A preventive method is more complex than a run-to-failure (or reactive) method. But it’s less complex than a predictive method.
A preventative method will involve things like conducting safety checks, cleaning parts, and replacing parts.
Checklist for Planning Maintenance
- Identify the assets that require preventative maintenance.
- Distinguish what kind of safety checks the machine will need.
- Assess whether parts need replacing or cleaning.
- Decide how regularly assets need checking.
- Create a formal risk assessment process to help the person responsible for checks.
- Talk to employees who work closely with equipment to discover more about how the machines are operating at the time of the check.
- Find out if parts need cleaning, lubricating or changing.
This checklist isn’t exhaustive. Instead, it gives you an idea of what you might need to do to plan your preventive maintenance procedures.
Machine Maintenance Logs
After completing any preventative maintenance, you should complete a log. This log entry should include a description of the work carried out, who carried it out and the date and time that it happened.
Your logs are also a good source of data which you can use when you want to know whether or not to fix or replace a machine. Use your logs to look at the time and effort it has previously taken an engineer to fix a machine. Then, you can weigh the cost of repairs against the cost of replacement.
Of course, your logs also provide you with a record of due diligence evidence in case a machine fault happens.
What to Read Next:
- 5 Key HACCP Considerations for the Bakery Industry
- 28 of your HACCP Questions Answered
- Good Manufacturing Practice Quiz
- Good Manufacturing Practice Online Training