Dust Hazards in Construction: Importance of Managing Risks & RPE
In 2022/23, the Health and Safety Executive (HSE) reported that there were 135 fatal injuries to workers – the largest number of these, 45, occurred within the construction sector. The HSE also reported that there were approximately 69,000 cases of new or long-standing work-related ill health reported by those working in the construction sector. This means that approximately 3.3% of all workers in the construction industry suffered from work-related ill health in the last year.
This article will look at one of the most common risks in the construction industry: dusts hazards. It will explain what construction dusts are, why it’s important to control exposure, and what actions employers should take to appropriately manage the risks posed by dusts in their workplaces and associated with their work activities.
What are the Dust Hazards in Construction?
One significant hazard that those working in construction are exposed to is dust. Exposure to construction dust can result in a range of serious ill health impacts, in permanent disability, and even death in those affected. These health hazards include asthma, Chronic Obstructive Pulmonary Disease (COPD), lung cancer, and silicosis. Therefore, it’s essential that risks from construction dusts are properly assessed and controlled.
Construction dust is the generic name given to dust that is found on a construction site. It usually refers to three main types of dusts:
- Silica dust. Silica is a natural substance present in many commonly used construction products, like bricks, tile and mortar. Silica dust is produced when construction and mineral processing activities are carried out on silica-containing materials, including sanding, cutting and drilling. These activities release very fine silica dust particles, known as respirable crystalline silica (RCS), which are fine enough to penetrate deeply into the lungs when breathed in. More information on RCS dust can be found here: What is Respirable Crystalline Silica (RCS) Dust and Why is it Dangerous?
- Wood dust. Wood dust can be created when carrying out work activities on hardwood, softwood and wood-based products.
- Lower toxicity dust, also known as non-silica dusts. These types of dusts are created from work activities on materials containing very little, or no, silica. For example, construction activities carried out on marble, limestone and gypsum.
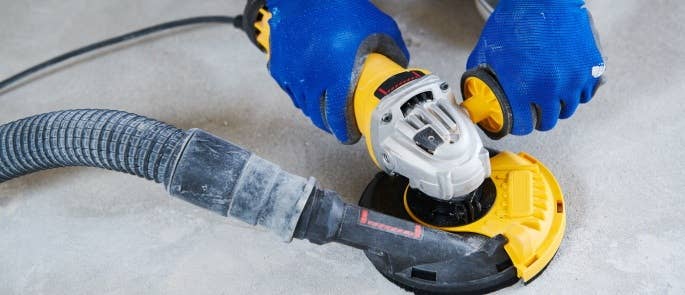
Why is it important to Manage the Health Risks of Construction Dust?
Exposure to construction dusts can have serious ill health impacts on anyone exposed. These include:
- Occupational asthma. Occupational asthma is an allergic reaction that certain individuals experience when exposed to ‘respiratory sensitisers’. Respiratory sensitisers are substances in the workplace, such as dusts, which, when an individual is exposed, can cause their airways to go into a ‘hypersensitive state’. When the airways become hypersensitive, exposure to even very small quantities of the substance can induce an attack.
- Occupational cancers. Long and short-term exposure to dusts can increase the risk of workers developing several different types of cancer, including lung cancer and cancers of the nose.
- Chronic Obstructive Pulmonary Disorder (COPD). COPD is the collective name for the group of lung diseases that result in breathing difficulties, including emphysema and bronchitis. Those with COPD often experience symptoms such as shortness of breath, wheezing, persistent coughing, and recurring chest infections. COPDs can occur as a result of prolonged exposure to fumes and dusts, and symptoms usually worsen gradually over time. However, individuals with COPDs can experience stages where their symptoms significantly deteriorate, very rapidly.
- Silicosis. Continuous, long-term exposure to RCS dust, or extensive exposure over a shorter period, can result in silicosis, a long-term lung disease. When RCS dust is inhaled into the lungs, the particles are attacked by the immune system, which causes inflammation. Repeated inhalation of RCS dust over a long period of time will result in fibrosis (areas of hardened and scarred tissue in the lungs) from the resulting attacking and inflammation that occurs. Silicosis impacts the lungs’ ability to function correctly, causing those with the disease to often experience a persistent cough, breathlessness and tiredness.
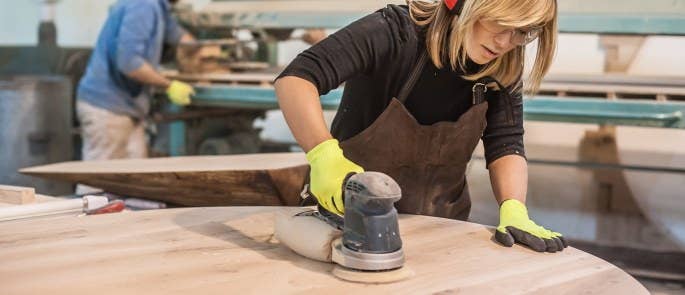
Construction Dust Exposure and the Law
Exposure to construction dust can have serious impacts on anyone exposed. Therefore, there are three main regulations that regulate exposure to dusts in the workplace. These are the Health and Safety at Work, etc Act 1974 (HSW Act), the Management of Health and Safety at Work Regulations 1999 (MHSWR) and the Control of Substances Hazardous to Health Regulations 2002 (COSHH). These regulations place key duties on employers to control exposure to hazardous substances in their workplaces.
Note: Some hazardous substances are not covered under COSHH as they have their own specific regulations, such as lead and asbestos.
Therefore, as an employer, your legal responsibilities include:
- Ensuring the health, safety and welfare of your employees so far as is reasonably practicable. Employers and self-employed are required to ensure that their work activities and workplaces operate in a way that does not pose risks to others.
- Carrying out a risk assessment to identify, assess and control the risks in your workplace.
- Recording the results of your risk assessment, if you have 5 or more employees. However, it’s good practice to record your risk assessment, no matter how many employees you have.
- Choosing appropriate controls to eliminate or manage exposure to hazardous substances as a result of your workplace or work activities.
- Sharing the results of your risk assessment with anyone impacted by your work activities, including employees, contractors and cleaning staff.
- Ensure that your work activities don’t expose workers to levels of hazardous substances above the Workplace Exposure Limit (WEL). WELs represent the legal safe maximum concentration of hazardous substances in the air, averaged over a certain time frame. There are around 500 substances that have WELs assigned to them. You can see a complete list of WELs in the HSE’s guide: EH40/2005 Workplace exposure limits. The only way you can measure exposure is by carrying out exposure monitoring. As an employer, you must measure exposure in your workplace and ensure that any WELs are not exceeded.
- Provide health surveillance for employees where necessary.
- Ensure employees are provided with adequate training in their duties and any control measures, so that they can work safely and effectively.
It’s important to note that this list of responsibilities is not exhaustive and that everyone involved in construction activities has legal responsibilities placed on them.
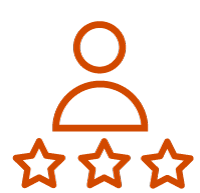
Need a Course?
Our Respirable Crystalline Silica (RCS) will provide you with more information on the legal responsibilities posed on various parties.
Managing Construction Dust Hazards
It’s important to remember that everyone involved in construction work has legal responsibilities to manage the hazards associated with their work activities. This includes principal designers, principal contractors, designers and contractors, small builders and employees.
The HSE recommends that you use the ACR model to assess the hazards associated with your work activities and to effectively manage the risks.
The ACR model involves three key steps:
One: Assess the risks – identify the hazards associated with your workplace and work activities and assess the risks. You must consider:
- The task itself. For example, consider the type of tools and materials that are being used to carry out the work activity.
- The conditions of the work environment.
- The duration and frequency with which a task is carried out.
Two: Control the risks – select controls to effectively eliminate or reduce the risks associated with your workplace and work activities. You must consider controls in line with the hierarchy of control. The hierarchy of control is outlined below:
- Eliminate the hazard. Consider ways in which you can eliminate the hazards. For example, you can eliminate dust-creating processes by ordering materials that are pre-cut, pre-prepared or pre-finished.
- Substitute for a less hazardous alternative. Consider if you can change the process or materials used to reduce the risks. For example, choosing wet methods over dry methods, such as using wet coring instead of dry coring, or using no-drill fixings.
- Engineering controls. Consider how you can alter or change the equipment used to reduce the risks. For example, could you use on-tool dust extraction, general mechanical ventilation or water suppression systems?
- Administrative controls. Consider how you can amend your work procedures to reduce the risks. Types of administrative controls include ‘designing out’ hazards, installing warning signs, enforcing job rotation and safe systems of work, and ensuring employees are appropriately trained in their responsibilities.
- Personal protective equipment (PPE). PPE should only ever be used as a last resort to reduce any residual risk to below an acceptable level. There is a legal duty on employers to consider the first four methods of the hierarchy of control to eliminate or reduce exposure to dust to below the workplace exposure limit (WEL). However, there are some situations where the use of one or more of the above controls can’t reduce dust exposure to below the WEL. Where this happens, suitable respiratory protective equipment (RPE) should be considered and used, alongside other controls, to reduce the risks to below the acceptable level.
Three: Review the controls – regularly review the controls used to eliminate or reduce the risks, to ensure they are in good working order and are effective.
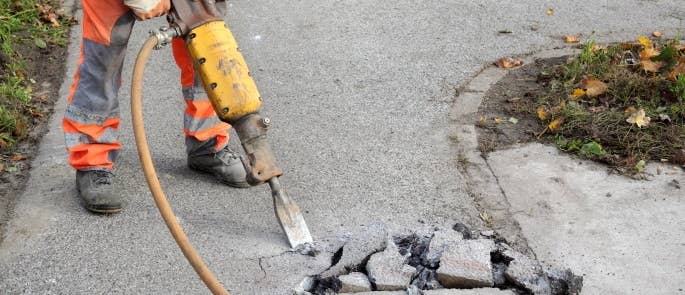
Types of Respiratory Protection for Construction Workers
It’s vital to understand that respiratory protective equipment (RPE) should only ever be used as a last resort. It should never be your first consideration when deciding on controls to eliminate or reduce the risks associated with dusts in your workplace.
There is a legal duty to use methods of elimination, substitution, engineering and administrative controls to eliminate or reduce exposure to dusts. However, there will be situations where using one, or a combination, of those won’t reduce exposure to below the relevant workplace exposure limit (WEL). If this is the case, adequate and suitable RPE should also be used to reduce exposure to below the WEL.
There are two main types of respirators:
- Powered respirators. These respirators use motors to pull air through the filter and supply the user with a flow of clean air.
- Non-powered respirators. These respirators rely on the wearer’s breathing to pull air through the filter and supply the user with a flow of clean air.
Respirators can be either tight-fitting (these have to be face-fit tested to ensure that they can make a good seal with the wearers face) and loose-fitting (these do not require face-fit testing).
It is essential to note that there are very important conditions for RPE use. Any RPE has to be selected carefully to ensure it is adequate and suitable for specific hazards posed by a work activity, suitable for the work environment and specific to the user (e.g. the correct size). More information can be found in the following HSE guidance document: Respiratory Protective Equipment at Work
Construction dust exposure poses significant hazards to workers. As described in this article, it’s important that you effectively manage the risks in your workplace. You can find more information on your legal responsibilities, common health hazards, suitable control measures and the ACR model in our Respirable Crystalline Silica (RCS) Awareness Training Course.
Further Resources:
- Ten Common Construction Site Hazards
- Health & Safety Training
- PPE in Construction: Safety Guidance and Checklist
- PPE Quiz
- What is Gypsum in Construction?
- Toolbox Talks in Construction: Guidance on Meeting Topics and Resources
- Protecting the Public During Construction Projects
- Respirable Crystalline Silica Awareness Training